No pressure builds up in the pump station. DIY pump station repair - possible malfunctions and their elimination
Residents of private houses, cottages, country houses are often urgently in need of installing a pump structure for pumping water from a well, well. For some, this is the only way to have water in the room. Therefore, when, one day, the pump stops buzzing, it is urgent to understand the origin of the breakdown.
If the pumping station stops pumping water, it is urgent to find the cause of the breakdown.
Often the stumbling block is air that enters the pump along with the fluid. Everything can be prevented, only initially you need to find out from which elements the pump structure is assembled.
Key components of the pump unit
There are many types of stations, but the basic components are inherent in everyone.
- Self priming pump. The principle of operation: the pump independently draws fluid from the recess using a tube, one end of which is in the well, the other is connected to the equipment. The pump is located a short distance from the water tank. The depth of the tube is also adjustable.
- All units are equipped with a hydraulic accumulator. The vessel, using the energy of a compressed gas or spring, transfers liquid under pressure to the hydraulic system. It accumulates hydraulic fluid and releases it at the right time, thereby avoiding jerks of water in the system. Outside it is metal, inside there is a membrane of rubber, a gas cavity filled with nitrogen is placed above it, and a sub-hydraulic cavity. Water is filled until the pressure in both cavities is equalized.
- Electrical engine. By means of the coupling, it is connected to the pump, and to the relay - by means of an electrical circuit. Due to the fact that the pump does not turn on for short fluid intakes, the motor does not wear out.
- Air outlet pipe.
- Collector element.
- Pressure gauge. It allows you to monitor the level of pressure.
- Relay. By changing the pressure, by the method of opening / closing contacts, it supports the independent operation of the equipment.
The main purpose of pumping stations is to support continuous pressure in the water supply structure. In order for all components to function like a clock, it is important to choose the right amount of accumulator and control the connection between the regulator and the pump itself.
Unit operation
When turned on, the first electric motor enters the business, it starts the pump, and it pumps the gradually incoming liquid into the accumulator. When the battery is full to the limit, excess pressure will build up and the pump will shut off. During the loosening of the tap in the house, the pressure decreases and the pump starts again.
When the pump structure is installed, it is connected to the pipeline, and the suction elements with a water intake device are placed in a recess with liquid.
The house has a battery connected to the water supply. The pipes are filled with water when the pump starts. When the pressure in the station reaches the desired peak, the pump shuts off.
The pump unit will solve the difficulty of supplying water to houses, baths, summer kitchens, outbuildings and other premises on the territory of your site. Having familiarized with the details of the station, it is necessary to study the possible causes of the failure of the device and methods for their elimination.
Failures that are most often encountered
In the process of using any equipment, a moment comes when it either wears out or breaks. So in the second case, it would be important for the owner to understand the causes of the damage. Here is a short list of reasons that disrupt the operation of the pumping station:
- no electricity - commonplace, but also not excluded, since the operation of the unit directly depends on the electric current;
- the pipeline is not filled with liquid;
- pump malfunction;
- the hydraulic accumulator is broken;
- damaged automation;
- cracks in the housing.
Popular issues and how to fix them
The pump turns, but does not pump water
What to do when the station does not pump water? A frequent cause of failure is a lack of fluid in the pipes or in the pump itself. It happens that the unit is functioning, but does not pump water. Then the tightness of the entire water supply should be inspected for places where the pipes are poorly connected.
Check that the pump is not empty. The non-return valve is not working properly. Bandwidth should be one-way. This is one of the most important parts of the station, because, after turning off the pump, it prevents water from draining back into the well.
Diagram of a pump station valve that may become clogged
It happens that the valve is clogged and does not physically close; debris, salt, grains of sand can get into it. Accordingly, the liquid does not reach the pump. We solve the problem.Before untwisting the unit, we recommend checking the voltage of the electric current. It happens that it is below normal, and the pump is simply unable to turn on. We check the presence of fluid in the water supply system and in the pump. In case of its absence, it is only necessary to add it to the pump through the prepared holes or to immerse the end deeper into the well for suction. Keep the gap between the water source and the pump within normal limits. If the pumping station does not shake, it is worth solving the difficulty of depressurizing the water supply system or replacing the check valve.
When, after all the manipulations, the equipment buzzes, but does not pump water, foreign particles get into it. To find out - unwind the pump and change its impeller or body. Sometimes only installing a new one will help.
Frequent Inclusions
Why did the pumping station turn on much more often? It turns out that it does not fully set the desired pressure and turns off. Therefore, it works in fits and starts.
There is a solution. When you notice that this happens, first check the hydraulic tank for serviceability. On the back of the tank there is a connecting tube, when it works correctly, when you press it, air comes out. If water flows instead of air, it indicates that a membrane has torn inside. Replacing it will work.
Another culprit in the lack of necessary pressure in the hydraulic accumulator may be a crack in the shell at the seam. Fix the hole in any way known to you.
Having checked, as it should, the tank, sometimes, it is enough only to independently pump the air in the required amount through the nozzle. Due to the fact that the joints of the suction pipe have openings, water will be supplied intermittently. It is important to examine it in detail and patch the holes.
The pump simply does not start
The primary actions are checking the current and normal voltage in the network. Next, examine the relay contacts. Burnt parts must be replaced. The winding should be whole. If you feel a special smell of burnt substances - the motor burned out.
Pump is buzzing but not spinning
When the pump starts, but does not rotate during power-up, the capacitor is broken, or the impeller could adhere to the shell. This is usually found in pumps that have been left unattended for a long time. In this situation, when the capacitor becomes unusable, it is changed. With the impeller is easier. It should be brought into action by mechanical action. Scroll hands several times.
The unit runs without stopping
We noticed that your pumping station is operating continuously, without stopping - here lies the violation of the pressure switch. Examine the device inlets. They can be blocked by pumped debris in the liquid. It is necessary to adjust its action, set the recommended pressure in the battery. First turn off the power and drain all liquid from the tank. Record the pressure level on the pressure gauge when turning the pump on and off. Remove the cover.
There will be two screws: the top is the larger one, the bottom is the smaller one. Large - adjusts the shutdown pressure. It must be turned in the required direction: either reduce the “-” pressure when turning off, or vice versa “+”. We turn on the power again and record the shutdown result. We perform this manipulation until we achieve the desired result.
A smaller screw adjusts the difference between on and off pressure. Its setting is similar to the setting of the top screw. It remains to find out her norm. The pressure difference is 1.0-1.5 bar. After adjusting the pressure, close the lid, draw water into the structure and connect to the network. Be extremely careful when configuring the relay.
Pressure switch circuit, improper operation of which can provoke a breakdown of the entire station
Incorrectly adjusted pressure can cause a breakdown of the entire system.
By aligning the pressure in the hydraulic accumulator, the user calms down and forgets to continue to monitor him. But the correct level of pressure will ensure the life of the membrane in the battery and, in direct proportion to the life of the entire structure.
In order to keep the pressure at the required level, it is necessary to measure the air pressure in the air cavity when the hydraulic tank is turned off. Turn off the voltage, open the tap next to the pump, and drain the liquid. Also, this procedure can be done when the unit has not yet been used in operation and has not been connected to the network.
We measure the pressure with a manometer. The main thing is that in the battery it was 10% lower than when starting the pump. Factory settings are usually 1.4-1.5 bar. So, if you have changed the level of the pressure switch, then by all means change it in the hydraulic vessel.
Provided that you did not interfere anywhere, it is still worth checking this level once a year. The main thing is to keep the pressure at the set mark. If it falls, it is easy to fix it with an ordinary tire pump, pumping air into the tank cavity.
It is recommended to monitor the excellent battery service. The liquid contains a small percentage of dissolved oxygen, which contributes to the progressive decrease in the volume of the rubber membrane in the battery. Inside, special valves are mounted through which excess air flows out. Therefore, it is required to remove fluid from the membranes once every 60 days. Before this, do not forget to turn off the electricity, drain the water from the tank (up to three times).
Prevention
In order to protect the pump from empty work, when no liquid enters it, so that the motor does not burn out, manufacturers came up with some ways.
- Float. The float cable is connected to the rupture of one of the phases supplying the pump. When the water in the well drops below the required line, the contacts in the middle of the float open and stop the equipment.
- Pressure switch with dry run protection function. When the water pressure drops below 0.4-0.6 bar, the connections diverge and the pump decays.
- Relays with flow sensor. When the actual flow of water is not carried out, the relay stops the platform.
- Level switch - an electronic board with three sensors, it is placed in a dry place, the house. One beacon remains on the board, the other two are lowered into the well. When the water level drops below the control beacon, it signals the relay and it turns off the power to the station.
It will cost less than replacing or repairing the entire station. Without delay, the preventive measures taken, the check of the pressure switch in the water supply structure contribute to the excellent functioning of the unit.
We hope you were able to figure out in what situations the pumping station does not pump water, the reasons and repair options.
The main element of any autonomous water supply system is a pumping station, which, like any other technical device, can periodically fail. In order to return the pumping equipment to working condition, you can use the services of specialized companies or do the repair of the pumping station with your own hands. However, before proceeding with the repair of such equipment, which is quite complicated in technical terms, it is necessary to identify the reasons why the water pumping station does not function.
There are many causes of malfunctions in the pump station. They can be associated with a lack of power supply, improper water supply from a water supply source, a breakdown of the pump itself, failure of a hydraulic accumulator, or elements providing automatic control of equipment. Many of these reasons that lead to the fact that water supply stations do not work or do not function correctly can be identified and eliminated at home, and professional skills and sophisticated equipment will not be required for repairs.
The device of pumping stations
Pumping stations, which are often called hydrophores, are now actively used to organize autonomous water supply systems for country houses and cottages, so the question of how to repair such equipment on your own, if necessary, is quite relevant. Before you understand how to do the repair of the pump station with your own hands, you need to understand what such stations consist of and by what principle they work.
A pumping station for equipping a domestic water supply system, which pumps liquid into the pipeline system, is installed on the surface of the earth, as close as possible to the well (as far as possible), and works from an electric power supply network. The main structural elements of pumping stations that ensure efficient and uninterrupted operation of such equipment in automatic mode are:
- the water pump itself, which pumps water from the well or well and pushes it under pressure to the outlet pipe (to equip the pumping stations, the surface pump is used primarily not submersible);
- water intake hose, which is immersed in water at the highest possible level;
- non-return valve that prevents water from the suction pipe from falling back into the well or well;
- a mesh filter installed in front of the non-return valve and cleaning the water pumped from the source of particles of dirt and sand, the ingress of which into the inside of the pump may become one of the reasons for its failure;
- the pressure sensor installed after the pump is located on the pressure line (the main task of such a sensor operating in automatic mode is to turn on the pump if the water pressure in the water supply system drops to a critical value and turn it off when it reaches the required parameters);
- a water flow sensor, which is installed before the pump and does not allow it to idle (when water stops flowing from a well or a well, such a sensor automatically turns off the device, preventing it from overheating);
- a manometer that allows you to measure the water pressure in the pipeline created by the pumping station.
Failures of the pumping station, as mentioned above, can be determined by a number of reasons, the exact clarification of which will allow you to quickly and efficiently perform repairs, returning the equipment to working condition. When diagnosing to determine the cause of a pumping station breakdown, it is not necessary to use sophisticated equipment and have professional skills. It is possible to identify most typical malfunctions of pumping stations both by external signs and by using devices that such equipment and a water supply system were originally equipped with.
Among the malfunctions of the pumping stations, several of the most characteristic can be distinguished, which each user is able to identify and fix independently, using the advice of specialists during the repair.
The pump is running but no water is entering the system.
When starting up the pumping station, it may happen that the pump with which it is equipped works and liquid does not enter the water supply. To determine why the pumping station does not pump water, it is necessary to analyze the individual parameters and operating conditions of the elements included in the equipment.
- First you need to evaluate the technical condition and the correct operation of the check valve, which is located on the suction pipe in the inner part of the well or well. Very often, the pumping station does not pump precisely because this valve is clogged with sand and dirt: without opening, it simply does not allow water from the well to flow to the pump.
- Check whether there is water in that part of the pressure pipe that is located between the pump and the well. If there is no liquid there, then, accordingly, the device has nothing to pump. Often this situation occurs when a power outage occurs and the pump station stops working. In order for the pumping station to start working normally again, it is enough to fill this part of the pipeline with water, for which a special hole is provided in it.
- It is necessary to check (with a disassembled pump) how large the output is between the inner walls of its housing and the impeller. The most intensive such production is formed in those cases when water is pumped, which contains a large amount of insoluble impurities (a kind of abrasive). If this is precisely the reason for the lack of water in the water supply system when the pumping station is running, it is necessary to repair the pump, which consists in replacing the impeller and the device housing, or its complete replacement. In the event that you find accessories suitable for the model of your equipment, you can repair the water pump yourself.
- It is also necessary to determine whether there is water (and at what depth, if any) in the well or well itself. If there is water in the source of water supply, then the problem is solved simply: just lower the supply hose or pipe to a deeper level of injection. In this case, it is necessary to observe the operating instructions for the pumping equipment in order to subsequently avoid repair.
The pump station runs jerkily
The pumping station, which operates in automatic mode, can often turn off and on, which indicates a malfunction. This nature of the operation of the pumping station, in which it is constantly turned off and on, is called jerking. This should be a signal to check (and, if necessary, repair) individual elements of the system.
If the pumping station operates jerkyly (it turns off, then turns on), the pressure in the air chamber of the hydraulic tank should be measured. To perform this procedure, you can use a car compressor equipped with a manometer. If this parameter is below the norm in the air chamber or pear for the pumping station, it must be raised using the same autocompressor. A repeated pressure drop in the air chamber of the device indicates that there was a depressurization of the system, the location of which must be identified. In the event that the joints have lost their tightness, then the accumulator repair is not required, just replace the sealing tape in such places.
The case of the hydraulic accumulator can also lose its tightness if a crack or hole has formed in it. It is not difficult to repair the accumulator with your own hands in this situation: for this it is enough to close the crack or hole that has been created using the “cold welding” composition.
Why is the pumping station often turned on and off during operation? The answer to this question may also lie in damage to the accumulator membrane. In such cases, the solution to the problem is to replace the accumulator bag or such a membrane.
Replacing the diaphragm in the accumulator
Unscrew the flange. Remove the membrane and clean the tank. The new membrane should fit the flange.
We insert and straighten the membrane, install the flange. Check the nipple and pump up the pressure. Check the pressure after some time.
Repair specialists often ask why the pump station often turns on or why the pump station does not turn off at a time when the pressure of the liquid in the water supply system exceeds the norm. This is usually due to a breakdown or malfunction of the pressure switch. Such malfunctions can also cause the pump station to not hold the water pressure in the pipeline. Repairing a pressure switch is a rather complicated procedure that can not always be done with your own hands. That is why in many cases they do not repair the pressure switches of the pumping station, simply replacing such a sensor with a new one.
Unstable pressure of the flow of water coming from the pumping station
One of the fairly common situations during the operation of pumping stations is the supply of water from taps with pulsating shocks, which indicates that the water supply system draws in air from the outside. To identify the place where air enters the pipeline, it is necessary to carefully check for leaks of all the connecting elements present in the area located between the well or the well and the pump station.
If the pumping station does not build up pressure or supplies water to the pipeline in a pulsating mode, this may also indicate that the water level in the source has decreased or that a hose or pipe of the wrong diameter is used to pump out the water.
When choosing a hose or pipe for placement in a well or well, it should always be borne in mind that their diameter should be the smaller, the lower the height of water intake from the source.
Pump station auto shut-off system does not work
The question of why the pumping station does not turn off automatically is quite common. A pump station operating in such a mode, which is considered emergency, cannot be operated; it should be immediately disconnected from the power supply. Otherwise, you may encounter a quick failure of the equipment, which means that you will need a more complex and expensive repair of hydrophore.
Why the pumping station does not turn off for a long time? The reason is incorrect operation or failure of the pressure sensor. A malfunction of this device, which operates in automatic mode, can cause the pump station to not turn on at the moment when the pressure of the fluid flowing through it decreases in the pipeline. In most cases, this problem is solved quite simply - by adjusting the sensor to the required pressure on and off the pump.
The pressure switch may not work properly for the reason that the elements of its internal structure are covered with salt deposits. In such cases, it is enough to disassemble the sensor and clean its internal parts from such deposits.
Pump station does not turn on
In most situations, the station does not turn on (and, accordingly, the pump-pump does not work) due to an open circuit, oxidation of the contact group elements and malfunctions in the pressure sensor. In addition, the causes of malfunctions can lie in the burnt winding of the drive motor, as well as in the failure of the starting capacitor.
With repair procedures such as repairing breaks in the power supply circuit of the station, stripping the contacts of the starting device and replacing the capacitor, as a rule, there are no problems. However, in order to rewind the electric motor, it is necessary to know how to disassemble it and how to replace the burned winding in it. That is why many users of pumping stations, when the drive motor burns out, simply replace it with a new one, avoiding repair.
Often when you start a pumping station, which has not been used for a long time, a characteristic hum occurs, but the equipment does not start to work. The reason for the occurrence of this situation is that the impeller of the pump of the pumping station simply “stuck” to the body of the device and cannot budge. In this case, it is necessary to partially disassemble the pump of the pump station and manually move its impeller from the dead center.
How to correctly install the pumping station
To less often ask why the pump does not pump water from the well or does not feed it correctly into the system, serious attention should be paid to the installation of the elements of the pumping station. The correct installation of water supply systems with submersible pumps is of no less importance, since repair of a submersible pump or its replacement is also an expensive procedure.
So, when performing the installation of pumping stations, one must strictly follow the following recommendations:
- prevent bending and deformation of pipes used for installation;
- ensure absolute tightness of all connections to prevent air leaks into the system;
- be sure to place a check valve and filter element on the feed pipe;
- immerse the lower end of the inlet pipe into the water in the borehole or well for at least thirty centimeters (the distance of the end of the pipe to the bottom of the water supply should be at least twenty centimeters);
This issue is relevant for many owners of country houses, since pumping stations often break down after the warranty period has expired. However, you should not panic, almost all problems can be eliminated independently.
Below we will look at a few common breakdowns and give advice on how to repair a pump station yourself.
The station works, but does not pump water
DIY pump station repair in this case, it consists in the diagnosis of the following elements:
- first check the check valve and the tightness of the pipelines;
- check if the piping connecting the well and pump is filled with water. The pump itself must also be filled with water ... (if the pump pumps less and less water, the reason may be the need to clean the well (flushing), as well filters can become clogged.));
- look if there is water in the well, lower the hose deeper into the well;
- the reason may be a low voltage, which is not enough for the electric motor.
The pump often starts, jerks
Take the pressure gauge on the automation unit. If the arrow rises to the desired pressure, and then drops sharply, there may be several reasons:
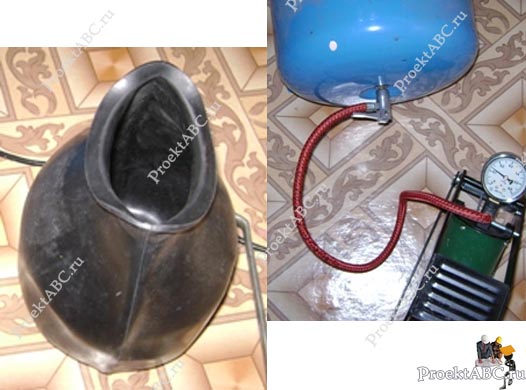
The pump pumps water, but does not turn off - how to repair
Pressure switch should be adjusted - dIY pump station repair It is necessary for the reason that over time the moving parts of the pump wear out and cannot create the required pressure, which was initially set at the factory. We are interested in a large spring, which defines the upper and lower limits for turning the pump on and off. The pressure must be reduced by turning the spring in the direction of the minus arrow.
The pressure switch must be cleaned, as sometimes salts are deposited, which clog the inlet.
Flowing pump
A possible cause of water leakage from the pump station may be a malfunction with the stuffing box. There are no gaskets there, but there is an oil seal, which can be of this kind (see photo below).
Knock bearings
It is possible to determine the bearing malfunction by tapping the pumping station using a plastic tube. Turn on the pump and, while putting your ear to one end of the tube, move the other to the intended bearing locations.
Pump does not turn on
There may be no power, check with a tester. Also, the contacts of the pressure switch could burn, in this case it is necessary to clean them.
If you feel an unpleasant smell of burned insulation, it means that the electric motor has burned. You just have to hand over the pumping station for repair.
Pump is buzzing and not spinning
If you turn on the pump after a long break in operation, it will be humming due to sticking to the body. You just need to twist the impeller of the engine, and then plug the device into the network.
The capacitor in the motor box may have broken. Using this capacitor, the device is connected to the network.
There is no equipment that never breaks, and pumping stations - even if they are from the most famous manufacturers, are no exception. What is very pleasing is that the causes of malfunctions often do not lie in the pump itself, and the problems are eliminated quite easily. What are they expressed in, and for what reasons?
This will tell our small instruction. And after watching the video in this article, you will find the answer to the question: “What if the pumping station for water supply does not work?”.
Correct connection is the key to success
Before you start talking about repair, it should be noted that with proper maintenance of the water supply system, which is done by yourself in the home, it may not be needed.
So:
- Initially, it all depends on the correct installation - and not only the station itself, but also the pipeline. Therefore, we will give a few useful tips for arranging a home water supply network.
Such important details
After all, what is it? This unit consists of a surface centrifugal pump with a built-in ejector and an induction motor, a membrane tank and several control devices. The power of the station depends on the number of stages in the pump, that is, the impellers.
By the way, all this can be put together and independently, individually selecting each element. The essence of the water supply system does not change from this.
- Another name for the membrane tank: accumulator. This is a tank of a certain volume with a nipple for air injection and a membrane, which, in case of damage, is not difficult to replace. The membrane tank is equipped with two pressure sensors - for monitoring the lower and upper values. It is at their command that the pump turns on or stops.
- A pumping station is traditionally connected to the mains supply via an electric cable (see). If the wire length provided by the manufacturer is not enough, you have to decide to purchase it yourself. It should be noted that the correct selection of cable for the normal functioning of the pump plays an important role.
- They do this with the help of existing tables, according to which, knowing the motor power, rated current and wire length, its cross section is determined. And since we are talking about the cable, we also recall the need to ensure its tight connection to the unit. It turns out to be of the highest quality when using inlet and shrink sleeves with mandatory grounding. One of the connection options is in the photo above.
- In addition to the cable, you also have to purchase elements for the suction pipe device yourself - these are either hoses (see) or pipes. Both of them should be reinforced, but this also has its own catch, as some of them are focused on rarefaction, and others on pressure. Their price depends not only on the length, but also on the option of reinforcing the product.
- When connecting the hoses, it is extremely important not to confuse their purpose, otherwise, vacuum may occur during suction. Typically, the hose is already equipped with a non-return valve at the factory, and when connected it remains only to tightly seal the place of its connection with the suction part of the pump.
- The pumping station itself must be firmly installed and fixed, and in winter it must be provided with the proper temperature conditions. The diameter of the pressure pipe should be related to its length: the further the feed is made, the larger the pipe size should be. And the fewer turns and taps on the water main, the more stable the water pressure in the system will be.
Problems typical for centrifugal pumps
First of all, before the initial commissioning of the station, the pump is filled with water. It is also necessary to bleed air through the plunger - a special device in the upper part of the body. When part of the air remains inside, the supply will either not be at all, or the pressure will be very weak.
At the same time, the operation of the station is usually accompanied by unpleasant noise:
- A decrease in pressure less than the nominal value also occurs due to clogging at any point on the suction system: the pump wheel blades, the filter screen or the supply pipe. Typically, installing a coarse filter on the suction hose helps to cope with this problem.
- In general, if we argue from the point of view of geometry, the pressure can be considered the height of the rise of water, which is carried out due to the energy generated by the pump. And if this distance exceeds the capabilities of the unit, then even the correct filling will not help him achieve rated performance.
- Simply put, if the station is designed to supply water from a depth of seven meters, then putting it on a well a ten-meter well does not make sense. Moreover, in such a situation, the phenomenon of cavitation (vaporization) can occur - and this has a detrimental effect on all the working parts of the pump, especially on the impeller.
Here, the temperature of the pumped liquid is also of great importance. With its increase, the suction height, due to friction losses, is significantly reduced.
How to protect the station from damage
Station pressure indicators are monitored by means of pressure gauges installed on both the suction and the supply pipelines. Deviations of their values \u200b\u200bin one direction or another, indicate problems, the cause of which should be ascertained as soon as possible.
- For the operation of the pump, it is very important that the shaft always maintains a given direction of movement. To prevent it from unwinding in the opposite direction, a check valve is placed on the discharge pipe.
- When installing the pipeline, it is imperative to make a bias towards the supply. This will prevent air from entering the water stream. Also, in order to avoid this problem, the suction pipe must be immersed in the liquid at least 50-80 cm.
- Longevity of operation to a large extent depends on the smooth rotation of the shaft. If appropriate measures are not taken when a run-out occurs, all seals begin to wear out intensively.
- The condition of bearings and seals depends mainly on the alignment accuracy. But, when it comes to the pumping station, you can not worry about this, since its elements are centered by the manufacturer during the assembly of the unit.
The main task of the station owner is to correctly calculate the diameter of the supply pipe. Then it will not create excessive voltage, which as a result is transmitted to the pump.
If you have problems
So, if the problems nevertheless appeared, we are looking for the cause of their occurrence, and take measures to eliminate it. For example: your pumping station runs jerkyly.
Here, most likely, the problem is in the accumulator. After all, what is he like? This is a sealed metal container, divided inside the membrane into two compartments - in one there is air pumped through a nipple, and in the other there is water.
- Moreover, the water does not come in contact with the walls of the container body, but is located inside the membrane chamber. This part is the most vulnerable part of this design. As a result of regular stretching and contraction, rubber loses its elasticity over time, or even breaks.
- If you see that the station spits out water, as it were, that is, it supplies it with high pressure, but in small portions, after which the pressure gauge drops sharply to zero, it is necessary to check the integrity of the membrane chamber.
- When, when you press the nipple of the air injection, water flows out of its hole, it means that the rubber part has broken through and needs to be replaced. There are no special difficulties here: the bolts are unscrewed, the old one is removed and a new membrane is installed. After reassembling, air is pumped into the chamber - and that's all.
- Sometimes the unstable operation of the station depends not on the integrity of the membrane, but on the pressure regulating device. It is expressed in the fact that the start-stop of the pump occurs too often. Often the pressure switch is clogged with dirt and scale, and it is worth cleaning it, as the problem of the pump can be solved.
- To understand the essence of the problems, you need to know how the pumping station works in principle. And the essence of its work is as follows: when the hydraulic tank is filled to the upper level, the pump is turned off. Its launch should take place not at the moment the crane is opened or, for example, the washing machine starts up, but when the water level in the chamber reaches the minimum value. This process is controlled by level sensors.
- And suddenly, the pumping station turns on at night, when no one uses water, and all the taps are closed. The conclusion suggests itself: somewhere there is a leak. Hence, an urgent need to revise the entire system. If there is no breakthrough in the pipeline, you need to inspect all connections for depressurization.
- Even a small leak is enough for the pressure to drop, and the station begins to run into operation uncontrollably. How to eliminate it, you need to be guided by the circumstances - it may be necessary to replace the flange, or perhaps you should rewind the thread and tighten the nut well.
- And here is another quite common problem: the water pressure has already reached the norm, and the station does not want to turn off. In this case, the cause may be an undervoltage in the network at which the pump motor is not able to reach the rated power. Check the voltage with a tester, and if everything is okay with this, most likely, the pressure switch settings were lost, or it failed.
- So that voltage drops in the network do not affect the operation of the station, it must be connected via a transformer. After all, not only a decrease, but also an increase in voltage can disable the pump motor. As for the reconfiguration of the pressure sensor, it is carried out by turning in one direction or another the regulator nuts located under the cover of the device.
- In conclusion, we will discuss the situation when water is not flowing from the tap when the station is started up. The problem, most likely, is that the pump performance clearly exceeds the well flow rate. Simply put, water consumption is higher than its natural inflow into the water intake.
In this case, all the taps must be closed and wait until the well is filled again. This, of course, is no way out of the situation. But if there are a lot of water distribution points in the house, as well as powerful plumbing fixtures like a jacuzzi or shower, it makes sense to think about deepening the old water intake or building a new one. Otherwise, you will have to reduce water consumption.